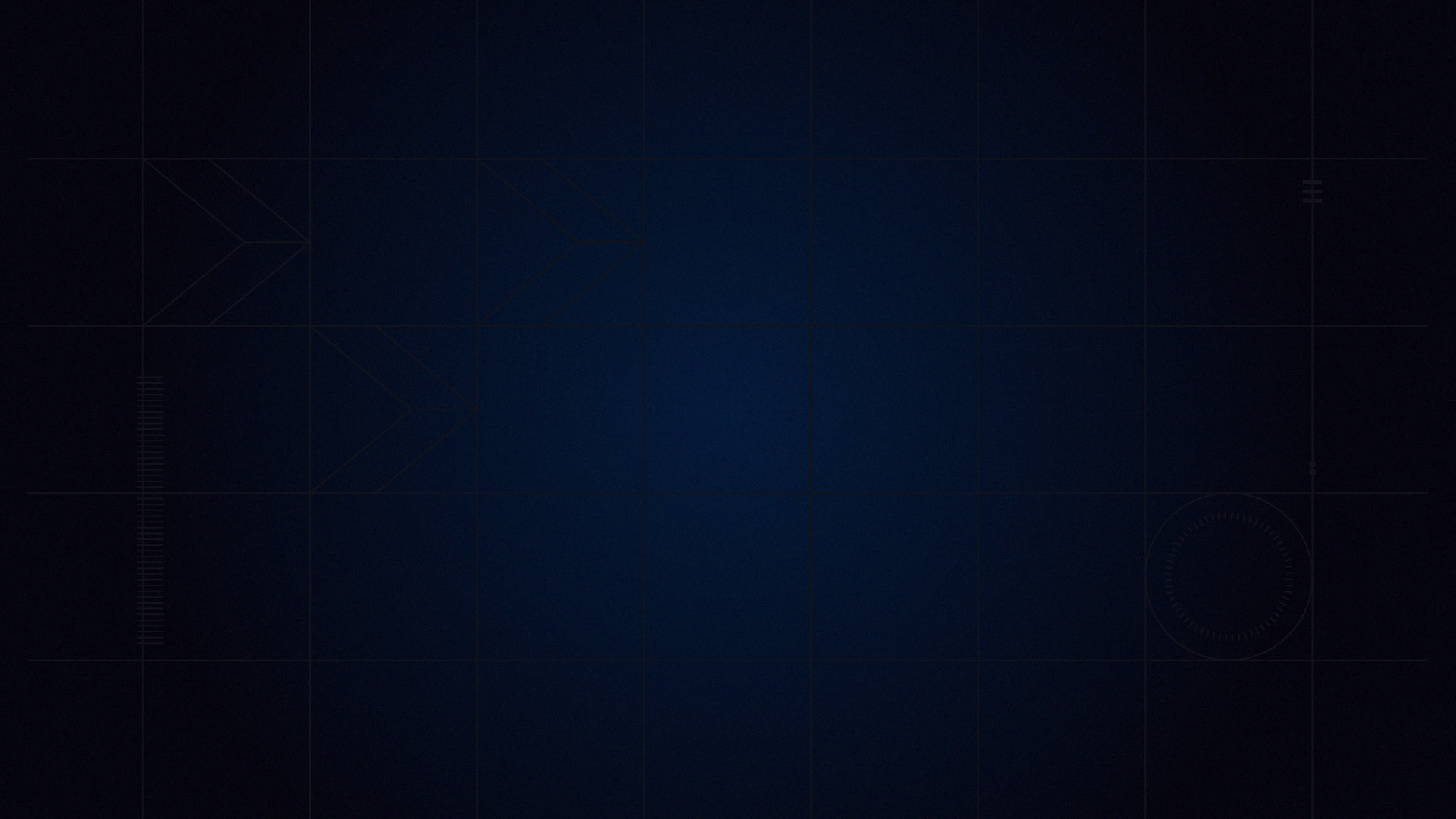
Commodore’s Garage #25 – Bumpstop Contact in Telemetry
June 16th, 2017 by Matt Holden
Last week’s build release put a stop to the coil-binding trend in the Class B series that had become widespread across the front-running cars. Eliminating all front springs below 500 lb/in took us away from binding by simply eliminating the springs that could bind under normal conditions, placing everyone firmly into the bump spring setup world and leveling the playing field across the series. This update is just on the heels of the Gen 6 update which did the same thing to eliminate both the coil-binding and pre-binding setups that were used, meaning both of the NASCAR cars are limited to bump spring front end setups, with the NASCAR Truck being the sole remnant of an abandoned setup era.
While the abandonment of coil-binding in the Gen 6 Class A series was largely a non-issue since coil-binding seemed to be limited to a small number of cars and teams, this has produced a big problem with the Class B series due to the low-rate springs of the past (less than 430 lb/in) all having the ability to bind before ever engaging either front bump spring. For many setups that utilized springs in the 300-400 lb/in range on the front, the bump spring was never engaged at all, leaving the drivers and setup builders to believe they were using the bump springs when, in fact, they were not ever touching them at all. In my Class B car prior to the update, I ran a 420 lb/in left-front spring and a 380 lb/in right-front spring. The 420 lb/in had enough travel to hit the splitter prior to binding, but the 380 lb/in would bind just prior to the splitter contacting the track, but after engaging the bump spring. Now, with two 500 lb/in springs being the minimum, most of your gains will be from tuning the bump spring rates and packer amounts, but the hurdle for this is determining when you have contacted the bump spring and when you have not.
This is the method I’ve used for a few years to determine the bump spring engagement point. I use MoTeC i2 Pro v1.1 and a custom Maths channel that isn’t very hard to configure at all, just follow the steps I have outlined here. I have exactly zero experience with Atlas, so if you have experience with it and know how to convert this method for use with Atlas, please let me know and I’ll add it into this article!
Finding Bump Stop/Spring Contact Point
First we need to know when the shock is going to contact the bump spring. Since the bump spring is mounted on the shock shaft and the height of the entire spring/packer stack is constant while on track, this means it will engage the bump spring at a specific deflection every single time. This consistency means it can be measured and traced to a fairly reliable amount, but the drawback is that it requires a bit of work and patience to get it working properly. This can be tedious, but it is invaluable, in my opinion.
We’ll start with these values highlighted in the above picture: Packer and Shock Deflection. For a quick refresher, the Packer value is how tall the shim stack is on top of the bump spring; Shock Deflection is how much the shock has traveled from full length. In our case here, we have 0.625” of packers/shims on top of the bump spring, and the shock deflection is 3.45”, meaning it has compressed 3.45” from full length. (NOTE: Starting deflection is irrelevant for shocks aside from knowing the available travel to the bump stop/spring because shocks don’t have a static force as with springs)
The image to the left shows how the shock is currently arranged on the left-front (click for larger version). We have a bump spring, packers, and a bump stop gap to the bottom of the shock. This is fairly common for all cars using bump stops/springs with a ride height rule, however there are some exceptions I’ll cover at the end of the article. At this point, note what your normal packer height is (0.625” for us right now) because we’ll need to reset it to that point later.
The image to the right (also click this for larger version) shows what we’re going to do with the packers now. We need to add packer until it contacts the bottom of the shock and physically moves the shock. Since the garage needs to reset and settle following a packer adjustment, it’s best to add two “clicks” of packers at a time and then Apply the changes. Whenever we have contacted the shock, the ride height will increase and shock deflection will decrease, meaning the shock has been pushed up by the additional packers. Once we’ve found the point of contact, we’ll reduce shims one at a time until the car is back at the ride heights we started at. The image below shows this process.
Doing this, we found that the shock was in contact with the packers when we had 3.000” of packers installed, but not in contact with 2.938” of packer installed because of the ride height change with the 3” packer height. Doing this will tell us how tall the bump stop gap is by simple math:
Bump Stop Gap = (Contact Packer Height) – (Starting Packer Height)
Bump Stop Gap = 3.000 – 0.625 = 2.375”
This means that the shock must travel 2.375” to contact the bump stop stack and engage the bump spring in the suspension. To find the value we need for the mathematical expression, we only need to add the bumpstop gap to the starting shock deflection (2.375 + 3.45 = 5.825”). We can now take this value and apply it to the channels in MoTeC to create a channel to show when the bump stop is actually engaging.
Creating the Maths Channel
In MoTeC, we’re going to go to Tools > Maths (or press Ctrl > M to bring up the menu). This is where we can build channels that are based upon mathematical formulas dependent on other channels. In our case, we’re going to depend on the Shock Deflection traces, named Damper Pos FL/FR on the stock cars. This is a different channel than is used on coil-over cars such as the Late Models, Modifieds, or all of the road racing cars, which use Suspension Pos channels.
Our mathematical expression is simply going to offset the Damper Position value relative to the bump stop engagement point, placing this point at 0.00” on the trace. This will create a display where any value over zero will be bump stop/spring deflection, and any negative value will be a disengaged bump stop. The expression is very simple, and takes almost no time at all:
- In the Search bar under the Tools section, search for the Damper Position channels by entering “Damper Pos”.
- Double-click the “Damper Pos LF” channel to place it in the expression box.
- Now, subtract the value we found for the bump stop gap from the Damper Pos channel to offset the trace. The final expression should look like this (using our value of 5.825” for the bumpstop contact point):
‘Damper Pos FL’[in] – 5.825”
The expression will need to be made for both corners of the car, so you will need to make a second channel for the Damper Pos FR channel as well. The final expression should look like this:
I’ve added a smoothing filter to my own channel to reduce some of the harsh bounces associated with higher-rate bump springs, but it is minor. It’s not necessary at all, so it’s your choice to use it or not. Once you’re done with your expression, click “OK” and “Close” on the Maths window.
Creating the Worksheet
Since the data set associated with bump stop contact is small, we don’t need a tremendously large amount of data on a worksheet to see what we’re looking for. Realistically, all you really need are the two traces, but it doesn’t hurt to add status lights that turn on when the value is greater than 0.00” (bump stop engaged) or a box to show the actual value. Further understanding can be gathered from a track map, speed trace, and even a Driver Marker channel to help diagnose issues on-track. Below is a picture of my own Class B car at Iowa showing the right-front bump spring engaged (and deflected 0.08”) while the left-front bump spring is not engaged.
Drawbacks and Issues
The biggest issue with this method is the need to manually re-calculate the bump stop gap whenever either Shock Deflection or Packer height changes independently of the other. Shock Deflection will change whenever Ride Height changes, which is caused by any of a thousand things in the garage, while Packer height is a manual adjustment. This can get a little tedious if you’re in the rough stages of a setup, but is very helpful for eliminating major issues with your setup.
This issue and need to re-calculate can be delayed (most times, at least) by making sure Packer changes are made to compliment a change in Shock Deflection. For instance, if the Shock Deflection increases by 0.250”, we need to decrease the Packer setting by 0.250” to maintain the same bump stop gap. However, it’s a good practice to always keep the setting up-to-date to eliminate the issues associated with this.
The Gen 6 Exception
As with many other things in the garage, the NASCAR Gen 6 cars have a unique exception due to their lack of ride height rules. For the Xfinity Class B cars, the bump stop gap is required to get around the ride height rules and keep the car low while on track. The Gen 6 doesn’t need to do this, however, and it’s often best to not have a bump stop gap at all to keep the acting spring rate as linear as possible. This can be achieved by simply adding packers until contact is made, and then leaving the packers at that height. Once aerodynamic forces take over, the car will be compressed enough that it will likely not disengage the bump spring, preventing the spring rate from changing suddenly in the center of the corner, as eagle-eyed readers probably noticed on my car at Iowa.
But this is soooo tedious…
Yes it is! As is the case with a lot of engineering problems, this requires a lot of detail-management to keep it correct for the current setup conditions. That said, you might notice a lot of things you didn’t notice before, such as bump stops disengaging at the exact point you keep spinning in the center of the corner, or the left-front bump stop never contacts at all and you can’t figure out why the car is plowing like a dump truck. It can be irritating to have to do this over and over in a single session, especially if you’re someone who likes throwing springs all over the car, but it is an absolutely invaluable tool to setting a modern stock car up. If you don’t know when the bump stops are in contact, you essentially don’t know what springs you’re running on! Take a few minutes and update the channel every once and a while and you’ll be amazed at the results.
~~~~~~~~~~~~~~~~~~~~
To keep up to date with The Commodore’s Garage, return to Sim Racing News every other Friday afternoon and “Like” our page at https://www.facebook.com/CommodoresGarage