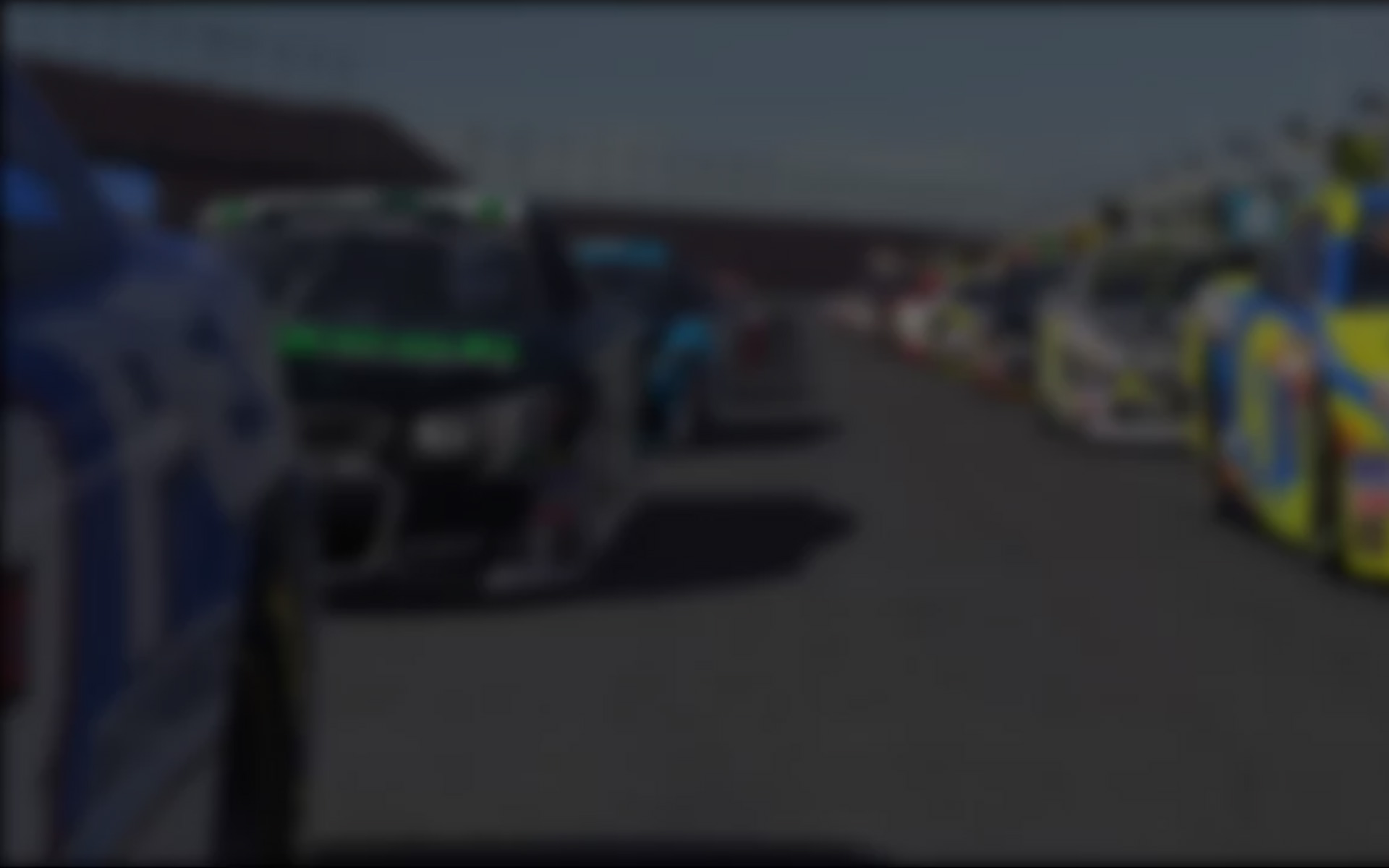
Commodore’s Garage #24 – The Dreaded Push-Loose
May 12th, 2017 by Matt Holden
All three NASCAR iRacing Series just finished a short-track swing, and during those weeks I saw, heard, got involved with, and was even asked about one of the most difficult phenomenon to understand in sim-racing: The “Push-Loose”. The series went to four of the most troublesome tracks to set a car up for, starting at Martinsville in late March then visiting Bristol and Richmond with Rockingham stuck in the middle for the Class B series. This week, the series went to Kansas, and the Class B series will make a lone trek to Homestead next week while Trucks the Class A series are off. All six of these tracks are wildly different in characteristics, but all of them can trick a driver into misdiagnosing a tight car as loose. We’re going to break away from the schedule the articles have been on and take a look at what’s going on with a “push-loose” condition, why it’s hard to diagnose properly in a simulator, and what to do to stop yourself from getting frustrated with this problem.
The Physics
A “push-loose” condition occurs when a car is experiencing understeer, or a “push”, in steady-state cornering and suddenly begins to oversteer, “loose”, on corner exit. For every tire in a given situation (speed, load, etc.), there is a maximum angle it can be turned relative to the direction of travel. Turning the tire will cause the contact patch to twist, and the angle of twist is known as the tire’s slip angle, and if the maximum angle is exceeded for a tire it will lose traction and begin to slide. Below is a quick chart that is similar to how a tire would exert lateral forces based on its steered angle:
While this is not an actual representation, it’s not an uncommon sight for a typical tire. As we increase the steering angle we get a higher lateral force to a point where the lateral force plummets past a specific angle. This phenomenon is the cause of most push-loose conditions, real-world or simulation. During the steady-state cornering understeer, the front tires would be turned past the maximum lateral force angle causing a loss of grip. As the car exits the corners, the driver will unwind the steering wheel and put the front tires back within their working range where they’ll magically regain traction. Despite the heavy loads on the rear of the car from corner exit due to banking, throttle application, and aerodynamics, the sudden switch in the front tires will break traction in the rear tires, causing a sudden oversteer condition on corner exit. It’s this combination of events that produce what is known as a push-loose condition.
The Simulation Issue
In my opinion, it’s nearly impossible to accurately simulate all of the sensations involved with a push-loose condition unless you have a remarkably sophisticated motion simulator. In sim-racing, the understeer portion typically goes un-noticed by the driver, and their diagnosis is a car that is loose off the corner. When I started sim-racing back in the mid-2000s, I had this same problem. It wasn’t until I began racing karts in 2013 that I truly understood why it was so difficult to diagnose a push-loose condition through a simulator.
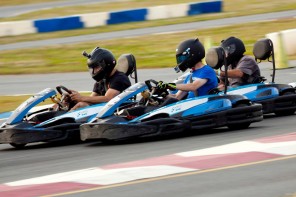
GoPro Motorplex’s old Sodi Rental karts weighed in at over 700lbs. They were great fun in a league-racing environment, but were very prone to snap-oversteer conditions. (Photo by Glenn Holden)
The kart pictured above is an older-model Sodi kart used at the GoPro Motorplex in Mooresville, NC for arrive-and-drive rentals as well as the leagues I raced in for a few years. They were extremely heavy (twice as heavy as my racing kart), had a high CG, and narrow front tires. All of this meant they were extremely prone to push-loose conditions when pushed hard, and it was in one of these kart-yachts that I experienced push-loose for the first time. The sensations for a push-loose are primarily felt through a combination of the seat and steering. Whenever I’m driving the karts and I think that it may be starting to understeer, I’ll make tiny movements on the wheel in the direction of the turn. For instance, if I’m turning to the right, I’ll tug the wheel to the right. If I don’t feel any increase in lateral g-forces, then the front tires have lost traction and the kart is understeering. It may not be plowing off towards the wall and could be tracking right along the inside kerb, but it’s understeering nonetheless. Once this happens, I’ll either prepare for the snap-oversteer on exit if it’s a short corner or unwind the steering a bit if it’s a longer corner. Regardless of the corner, it’s much easier to manage and prepare for. On my racing kart, where the front tires are exposed and easier to hear, the sliding sound is enough to tell me I’m about to have a tremendous event whenever I reach corner exit.
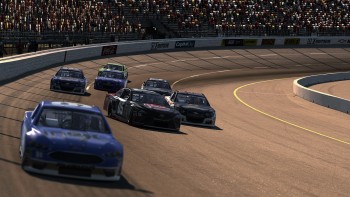
Nick Ottinger’s Richmond car in this week’s NASCAR PEAK Antifreeze Series race showed every sign of having a push-loose condition.
In a simulator, the seat-of-the-pants feel is missing, and what’s left is a combination of visuals and sounds. This makes it extremely hard to diagnose this on-the-fly since the lateral g-force is missing from driver feedback. Drivers frequently mis-diagnose a push-loose as simply loose, and it’s nothing to be embarrassed about. Nick Ottinger, whom I’ve worked with for nearly six years in sim-racing, was unable to diagnose a push-loose condition in the first couple of years while he was running in the Pro and WC Oval series. Today he can do it extremely well, and has gotten to where he won’t immediately say the car is loose or tight, but will instead take a few laps to figure out how it’s getting to those loose or tight conditions. A great example would be this week during the NASCAR PEAK Antifreeze Series race at Richmond, pictured above. The rear end being hung way out of line during the first quarter of the race was frustratingly common, but instead of telling me the car was loose, he asked for the car to be raised up at both ends because “The splitter’s hitting and it’s pushing in the center.” When I asked if that would fix his exit, he said, “Yes”. Having the splitter touching the track was unloading the front tires, creating a push in the center of the corner, then the rear end would swing around when the splitter raised up on corner exit, loading the front tires.
Diagnosing the Problem
Despite not having a lateral-g sensation in a simulator, it’s possible to still take what you are given and realize you’re experiencing a push-loose condition. We’re still given excellent cues from audio in the form of tire scrub noises as well as the engine in some cases, visuals, and even tire data. It’s all subtle, but effective nonetheless.
The most obvious visual for a push-loose condition is the point where the car begins to spin. In almost every situation where an oval driver says “It’s spinning when I come off the corner”, it’s a push-loose condition. This is often the case due to track banking falling away and the car spinning once it’s reached a flatter straightaway. Bristol and Richmond are exceptionally bad about this because of the large banking shift at both ends of Bristol and the 2° backstretch at Richmond. It’s not limited to short tracks though, as Texas is well-known for its very difficult turn 2 exit with a relatively early banking transition. In the picture of Nick’s event at Richmond (above), he’s all the way out of the corner when his car began to step out on him, a tell-tale sign of a push-loose condition. If the car is relatively stable all the way to corner exit before it suddenly wants to misbehave, it’s most likely a push-loose condition.
The other obvious sign is from the tire data itself. Below are the temperature numbers from one of Nick’s NPAS cars that was showing a push-loose condition during the race:
I’ve averaged the tire numbers under the I/M/O trio to make it a little easier to see what’s going on with the car. From the averages, it’s immediately apparent that the car is mechanically tight, with a heavily-loaded right-front tire and a largely unloaded left-front tire. We’ve also got some pressure issues here, but that’s going to take a backseat to the bigger problem. The major thing here is the near-16° difference in the right-side tires, and the 29.5° difference in the left-side tires. We have a problem here.
Probably the only time I’ll ever record tire wear numbers is when a push-loose condition is expected. We know from the temperatures that the right-front and left-rear were very hot, suggesting a tight car. Normally, when those numbers are high like they were, we’d expect the hot tires to be worn significantly due to over-loading. However, we can see above that this is not the case, and the rear tires were worn more than the front tires.
Mind blown, right? We have hot tires that aren’t worn, and cool tires that are, which breaks some rules. This arrangement is the hallmark of a push-loose condition, and is present every time this happens. The right-front tire is slipping, but not necessarily sliding, and is producing a lot of heat because of that. On corner exit, once the front tires regain traction, the rear end of the car loses traction, wearing the unloaded tires, causing them to wear.
Adjusting the Car
Unfortunately, when you’re first learning to see these problems and feel what’s going on, it’s going to be difficult and it’s not uncommon to make a few mistakes along the way. The key is to not get frustrated and simply take a look at what you are given and figure it out from there. The hardest thing to mentally adjust for is to have the car spinning on you unpredictably and force yourself to loosen the car up instead of tighten it up. The two most effective adjustments for a push-loose condition are found in the rear of the car. Apologies to the road-racing crowd, but one of them is limited to oval cars.
- Raise the right-side of the track bar. I heard a NASCAR crew chief say “Tight in the center, loose off? Raise the track bar one round”. It works, and how much you want to raise it is up to you.
- Rebound on the inside rear tire. This magic adjustment directly affects the car’s crossweight in transition cornering such as corner entry. A higher rebound value on this shock will decrease the crossweight approaching the center of the corner, freeing the car up and potentially curing the loose-off condition.
This unique condition is also the precursor to a lot of fundamental issues with your chassis setup, and it’s not uncommon for us to start fixing one problem only to find five more. Unlike having a car that is just plowing on entry or trying to face the other direction in the center of the corner, there are a lot of issues combining into one giant headache here, and rarely is it going to be limited to one single adjustment. In the tire data from Nick’s car earlier, I pointed out that there were tire pressure issues. There were also alignment issues, chassis balance issues, and overall spring package issues that were present in that car. I didn’t outright fix his issues during the race, I simply made them more tolerable. We’re taught the old adage “If it hits the wall with the front, it’s tight; If it hits the wall with the rear, it’s loose”, but the level of over-simplification in that is astronomical. In the older days of motorsport, backing the car into the wall was usually cured by softening the rear springs and all was well. Today, when we combat the magical forces of aerodynamics and chassis dynamics, we have to start looking deeper into the problems we encounter on track to figure out what is really happening in our cars.
~~~~~~~~~~~~~~~~~~~~
To keep up to date with The Commodore’s Garage, return to Sim Racing News every other Friday afternoon and “Like” our page at https://www.facebook.com/CommodoresGarage