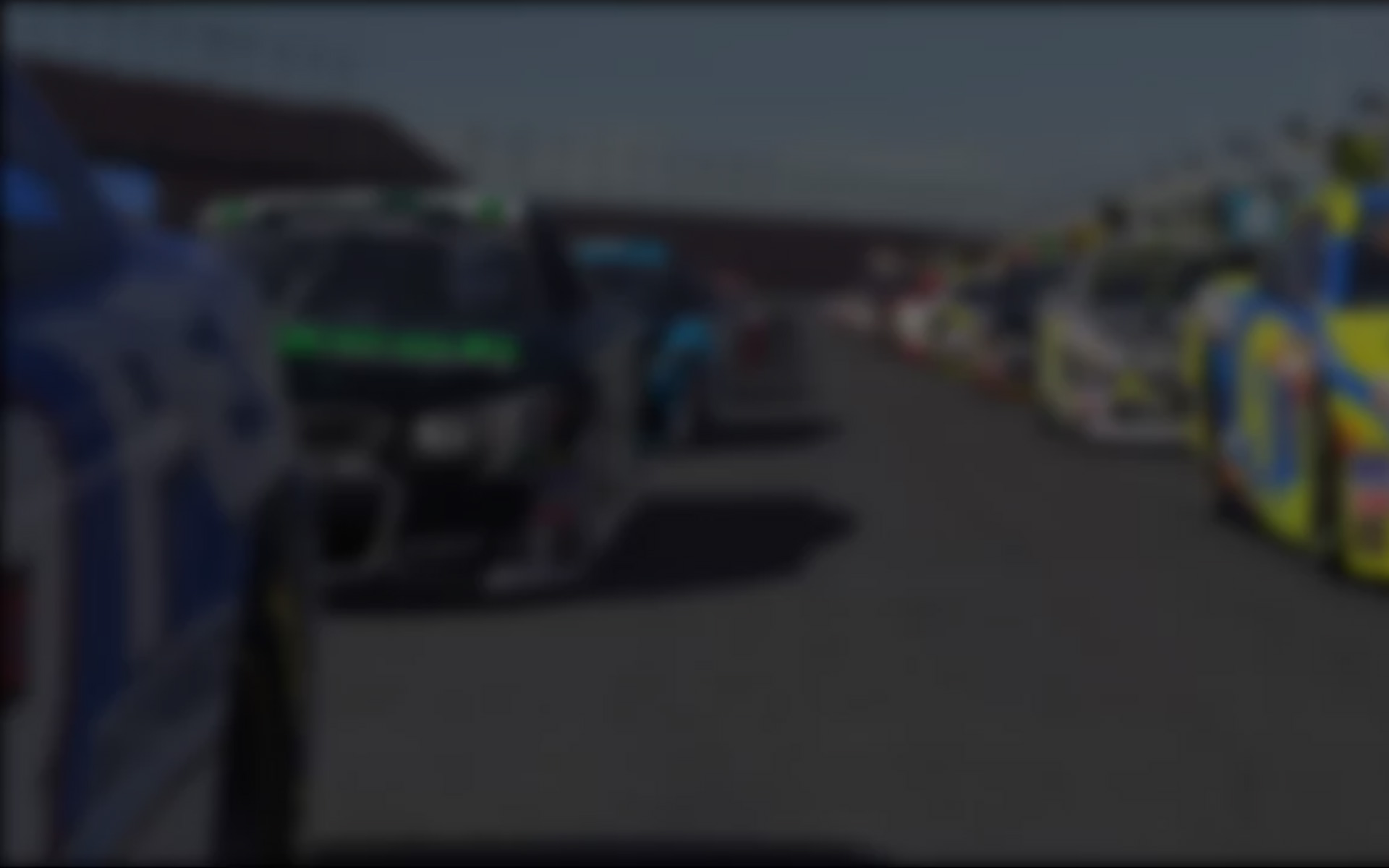
Commodore’s Garage #18 – Implementing Bump Stops
January 27th, 2017 by Matt Holden
Of all the things available to us in the sim-racing garage, the most confusing thing is typically the simplest component on the car: The bump stop. Ironically, the bump stop is just a tiny version of the one thing that almost everyone understands: springs. The confusion doesn’t come from its characteristics, but instead from its operation and how it affects various parameters in the car’s behavior. Many cars in the iRacing service use bump stops in some way, and each car’s method is unique in some way. Despite that, like everything else, they are all governed by the same rules of physics. The rules for the Mercedes GT3 car will work on the NASCAR Super Late Model.
What is a bump stop?
For a quick refresher, check out the first Commodore’s Garage article on bump stops, linked here: https://www.iracing.com/commodores-garage-9-bump-springs-2/ That article is a generalized view of the bump stop/spring component as a whole, and now that we know more about how springs work, it’s time to go into a little bit more detail to fully understand them.
To begin, we need to know where they are on the car. In almost every case you’ll come across, they’re located on the shock absorber regardless of where the main spring is mounted. Some passenger cars have a bump stop molded into the lower suspension arms, but for racing purposes they’re always going to be mounted on the shock to make it easier to adjust and/or replace the components to the bump stop.
The first component is obviously the bump stop itself. The most widely used type of bump stop is a composite, foam, or rubber shape that will come into contact with the shock body at some point in the shock’s travel around the race track. These can come in a variety of shapes, from the square-sided “puck”, the “donut”, or even the “Christmas tree” common on some oval short track cars. While the shape is irrelevant for us, it actually changes how the bump stop exerts forces as it is compressed. While a steel coil spring produces a linear force increase through travel, composite and rubber bump stops do not, and instead produce a rate increase through travel.
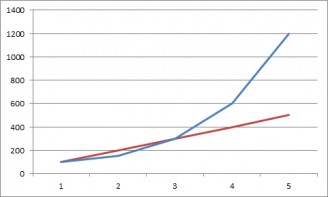
An example of how a bump stop will gain rate and force through deflection when compared to a spring. In the above graph, the blue line represents an exponential increase from a rubber bump stop, while the red line represents a perfectly linear coil spring.
This is an example of the difference in how a bump stop will differ from a spring in its operation. The red line represents a simple 100 lb/in spring. The increase in force is linear, with each step in deflection increasing the force by 100 pounds. The blue line represents how a bump stop would behave, but on a tremendously large scale (There’s no bump stop on this planet that will compress 5 inches). Instead of a constant increase in force, we have an exponential increase in force due to a gain in rate through travel. Note that the change from “4” to “5” is the same increase as from “1” to “4”. Not all bump stops will follow this exact curve, but it’s not very different from what is common in racing. This is extremely important to understand when choosing how to use the bump stop in your car.
The other component to consider is a packer, or a shim. These are used to change where the shock body will contact the bump stop in travel, and thus use the bump stop as part of the suspension. When the shock is not in contact with the bump stop, the bump stop is just extra weight on the car, but having the contact set properly can make a car handle perfectly and having it wrong can make it handle like a dump truck.
Packers are very simple, usually just plastic disks that sit on top of (or below) the bump stop.
The combination of both the bump stop and the packers can be referred to as the “stack”. Here’s an image of a typical bump stop arrangement on a modern shock (click for larger image!). I’ve highlighted the bump stop (consisting of three “donut”-style bump stops), the packers, and the bump stop gap.
What about Bump Springs?
Bump springs are a relatively new invention and have seen a tremendous wave of adoption in oval racing. Since rubber bump stops have the issue of rate change, this can lead to handling inconsistencies around the track. Bump stops at the NASCAR Cup Series level could be extremely stiff, in the tens of thousands of pounds-per-inch, and tiny changes in compression (even 0.05” in some cases) could result in a tremendous change in acting spring rate on the wheel. Imagine going from a 500 lb/in right-front spring to a 6500 lb/in spring without warning in the center of the corner and you have the issue. Not to mention that building the shocks for these very specialized bump stops was getting expensive, and lower-budget teams would struggle to get everything arranged properly in the car. Even at the local short-track level, having a bump stop gap off by a few tenths of an inch could be the difference between a front-runner and a back-marker.
Enter: The bump spring. In real-world applications, these come in two forms, Coil spring and “Belleville” dish-springs, but that doesn’t need to be considered for sim-racing. Since these are simple springs, they produce a linear force increase through travel instead of changing rate randomly through travel. This simplifies the physics and mathematics involved and produces an extremely consistent spring rate through the entire range of travel. Right now, only the NASCAR Xfinity and Cup cars use rate-adjustable bump springs, while other cars either use composite/rubber bump stops or the rate is not adjustable.
Here is the same shock as mentioned previously, however with a bump spring substituted for a bump stop. As you can see, it’s exactly the same! The only difference is how rate varies through travel. We still have the same packers and the same bump stop gap, and for simplicity’s sake, the same bump stop height. The physics and ideas involved with both stay the same: Both add an extra spring to the suspension, both produce an increase in wheel rate, and both can be used to stop downward travel.
What does it do?
Initially, bump stops were used to do what their name suggested: stop bump travel. Early uses were often to overcome ride height rules, most prominently during Formula 1’s ground-effect period by using soft coil springs to drop the car under aerodynamic load but stop it from dropping further once the car had reached the perfect height for aerodynamics. They’ve evolved since then, and engineers have discovered they can also be used for acting spring rates as well, most often in cars lacking a “third spring”, such as GT cars, sports cars, and oval-track racing.
The need for these arises from a trend toward aerodynamically-based chassis setup. For good aerodynamics, we need stiff springs to keep the car low to the track but not in contact with the track. Sanctioning bodies impose minimum ride heights for whatever reason, and these heights are typically far beyond what is desirable for aerodynamics. Cars need to drop down below these heights at speed, but that requires a soft spring. The bump stop will eventually contact the shock, and now we have the stiff springs necessary for aerodynamics, as well as the low ride height to go along with it.
Mechanically, bump stops behave in the same way a spring does: External forces will compress the bump stop once it has made contact with the shock, the bump stop (or spring) will compress until the force it exerts equals the external force, and the suspension will travel no further. The unique aspect of bump stops is that the wheel rate can change dynamically through travel as the shock comes into contact with the bump stop and releases the bump stop.
For example, let’s consider a coil-over vehicle where the spring, shock, and bump spring (for simplicity) all move on the same axis, and thus a 1:1 motion ratio exists between the main spring and the bump spring. Our main spring for this will be 250 lb/in and the bump spring is 1250 lb/in. We’ve set our bump stop gap to be 1.5” from static ride height, and we’ll just keep the 1:1 motion ratio going between the wheel and the spring. For the first 1.5” of travel in the suspension, the wheel rate will be 250 lb/in. Once we come into contact with the bump stop, we now have to add the two springs together, and the wheel rate jumps to 1500 lb/in for any travel beyond that point. This is a major jump in wheel rate, and definitely something that a driver would notice in the car. Compression is no problem, but an improper arrangement of sway bar and shock could cause the shock to contact and “release” from the bump stop multiple times through a single corner, especially on a bumpy surface. Coming on and off the bump stop many times in a corner results in multiple changes in spring rate through the corner, and there’s never a good ending for that situation.
Packer Settings
The packers are a tremendously important part of the entire bump stop stack and I could do an entire article on them alone. As the car compresses and gets to where the shocks contact the bump stop, we have a lot of things that are happening. Sway bar preload and spring forces at this point, just prior to bump stop contact, will result in a “dynamic” crossweight that is likely different from the static crossweight. Once the bump stops are in contact, the crossweight can change yet again, and this is a problem. If the packers aren’t set properly, then bump stop contact can send the dynamic crossweight in one direction very quickly, which is often perceived as an issue stemming from spring rates or sway bar settings. For instance, if the right-front bump stop contacts earlier than the left-front, there will be a sudden increase in dynamic crossweight, or vice versa if the left-front bump stop contacts first. Due to the high rates used in bump stops, it’s unlikely that the second bump stop will be able to “catch up” to the first one.
Timing is everything when using bump stops. If the shims and bump stop gap aren’t set properly, it’s very easy to get bogged down looking for a problem that you’re never going to solve. Most of the cars on iRacing have symmetrical suspension systems, so if the packers are set equally on both sides, there’s a good chance the bump stops will contact at the same time. The NASCAR Xfinity and Cup cars are asymmetrical, however, with the right-front shock usually slightly longer than the left-front shock. As a result, it’s good practice to keep the shims at the same height for rough tuning and for clearing any contact with the race track, and adjusting one shim by a small amount at a time to tune the car’s handling once on the bump stops. Usually a difference of 0.125” between each bump stop stack is safe and will produce a consistent behavior without major headaches and issues coming your way.
Special Cases: V8 Supercar & the NASCAR Cup Car
The V8 Supercars got an overhaul in the last build that introduced Damper Length and Bump Stop Gap to the setup screen. Damper Length itself isn’t a new concept to the iRacing setup garage as a few cars have had this option for a while. The V8 Supercar adds in the complexity of both a shock collar offset and the bump stop gap, and the three have to be adjusted at the same time to change the car’s handling. If the V8 Supercar is your wheel house (If it isn’t, try it, it’s fantastic), the only way to understand this is going to be fiddling with it yourself. The proper way would be to adjust the damper length, then adjust the shock collar to reset to the previous ride height. If you did it right, you should have the same ride heights with a new bump stop gap!
The other special case is the NASCAR Cup Car. Since the car doesn’t feature ride height minimums, the concept of the bump stop becomes more complex. There’s no need to “drop” the car at speed, so the reasoning for a bump stop/spring changes. In the future, we’ll go over what this adds to the mix and the various ways you can go about setting that specific car up.
~~~~~~~~~~~~~~~~~~~~
To keep up to date with The Commodore’s Garage, return to Sim Racing News every Friday afternoon and “Like” our page at https://www.facebook.com/CommodoresGarage