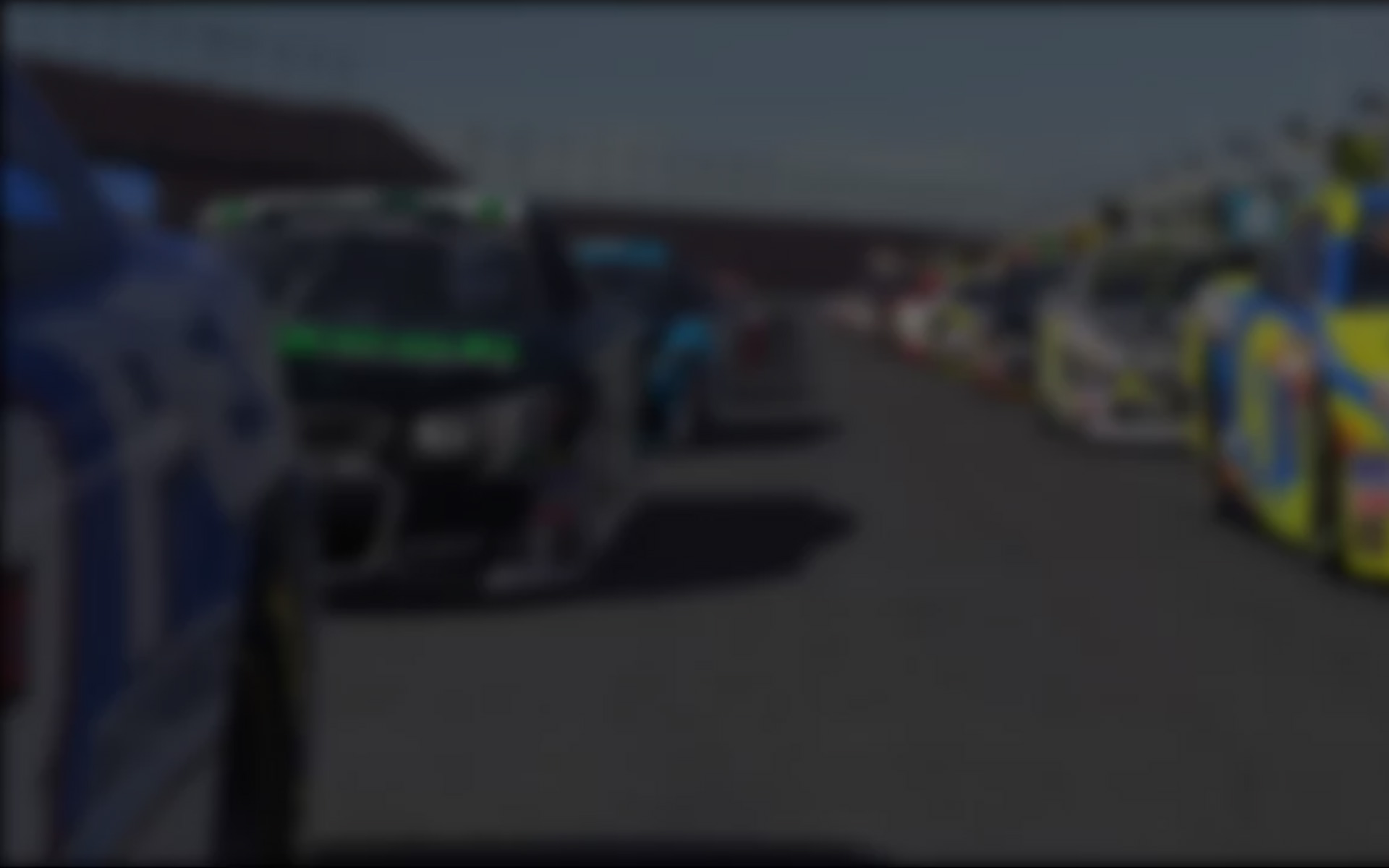
iRacing’s Corvette: Good Enough is Not Good Enough
January 8th, 2010 by Jaime Baker
We’ve gotten approval to build the Pratt & Miller Corvette C6.R GT1 car! SWEEEEET! OK, what’s first? Hmmmm. Dyno sheets. That’s the most important thing, right? That beautiful sounding motor, deep and rumbling, with earth-moving torque and acceleration. Now that sounds like fun!

iRacing.com's Corvette C6.R: Sounds like (and is) fun.
Getting the power to the ground is next, so what gearbox does it use? What are the various gear ratios? How many options of gear ratio, and what’s the layout and the inertia of all the components? Xtrac builds the box, and my friends at Xtrac USA have been exceptionally helpful with data for component inertias in the past, maybe they’ll provide me with additional values…
And it’s got wings, well, one, and it’s HUGE. That must make a TON of downforce. But then there’s none on the front, and they’re not allowed to use an enormous splitter or multiple diveplanes, so how much of that rear wing can they actually use? I guess get the front end to work, and balance it with whatever wing position works, then.
I’ve also heard this car generates a ton of downforce. I just read an article in Racecar Engineering that said it made as much as 1800lbs of it, so 0.9 tons actually! I’d say that’s BARELY an exaggeration, then.
Oh, but it’s supposed to handle amazingly well too, so I guess we need all the suspension motion data. Camber gain, spring rates, wheel rates . . . all that stuff. I guess damping rates are needed as well, since we have springs that need to be controlled.

From WinGeo3 to virtual C6.R, a combination of precise data, painstaking calculations and educated assumptions.
But what are the sprung and unsprung masses? What are these items you ask? Sprung mass is anything that the springs hold off the ground. Unsprung is anything that follows the road surface, like the wheels (with tires) and the suspension (well half of it anyway, the ends that are attached to the wheel). And now that we’re worrying about masses, that leads us to inertias. How much inertia for the sprung mass vs the inertia for the whole vehicle? Does that data exist? How was it determined? If it doesn’t exist, I get to break the car down into smaller individual components and take my best shot at calculating it all. Fortunately, most of the bigger teams/manufacturers have a good handle on the inertias so this time it’s pretty easy. No more than a few hours to get the numbers laid out with a variable fuel load.
What about the masses and inertias in the engine and driveline? Thanks to Xtrac USA, the gearbox is easy. The engine? Not quite so simple. General Motors is not going to give me those numbers. Not a chance. So now I get to calculate all the inertias for all the moving parts within the engine.

Exhibit A: C6.R by Pratt & Miller or iRacing.com? (See below)
So how much does a 7.0 liter engine crankshaft weigh? Thanks to Google (a wonderful source of arcane information), it appears that a Chevy 427 crankshaft weighs approximately 53-57 lbs. How much lighter than that is the factory race version? I figure it doesn’t rev very high, and with all that torque it needs to be tractable, so super light isn’t really necessary, so let’s go on the high side of the range at 56 lbs. And that crankshaft is tough to calculate. Draw a crankshaft, break it down into all the individual sections that are symmetrical and try to get a rough estimate to work using the material density and mass, and you’ve got a decent approximation. But that’s still just a guess. An educated one, but still a guess… Con (connecting) rods are fairly well documented (online) at approximately 480 grams. Pistons? 540 grams there…
What about chassis and suspension component inertias? Yup, I get to calculate those too, but this time Pratt & Miller have provided the masses of the individual components and a total inertia for several assemblies, as well as the whole vehicle from their own shaker rig testing and CAD data. That makes it much easier to be within the 2-3% error I’ll accept. (Much more than that, and I have to dig deeper to try to locate any assumptions that may not be correct or outright miscalculations. It’s happened before, and it’ll happen again, but that’s the challenge!)

Exhibit B: C6.R by Pratt & Miller or iRacing.com?
What about aerodynamics and downforce now? What’s the “perfect” ride height and rake to maximize downforce and minimize drag? How about lift to drag ratio? Is that what we want to optimize? Or is this thing stout enough that it’ll overcome most any bit of drag with all its torque and just go regardless? If that’s the case, balancing the downforce front-to-rear is really the key. With the rear wing trimmed out to the available minimum, there’s less than a 10% drop in drag, so clearly most of the drag is in the body, and the body lines are quite clean, with a very smooth underbody helping to keep it nice and slick. That means a relatively small difference in top speed from min to max rear wing with this car. But min rear wing also means the aero balance shifts forwards making the car quite loose. Sounds exciting in a video game…not a good scenario at 190 mph in real life! As long as that front-rear aero imbalance gets adjusted, then it’s fine and it’ll gain you about 5mph at top speed. Like I said, it’s small at roughly a 2.6% increase in top speed, but you trade-out 6% of your downforce. Is that a worthwhile trade? How long is the straight at this track you’re racing on? Are you going to get anywhere near absolute top speed?
(Seeing as I have the benefit of seeing the aero equations, and a few setups straight from the manufacturer, I can clue you in to the rough setups. 2.5 to 3 inch front ride height, and 0.5 to 0.75 inch rake with fairly stiff springs to control ride height and pitch are what seem to work well.)

Exhibit C: C6.R by Pratt & Miller or iRacing.com?
This is all well and good, but what is the MOST important element of any car? The tires! Let me just pick up my phone and call Michelin. They don’t recognize my name? And they won’t give me all their tire data? Why not!?! It’s only years of data they’ve developed and paid for with their research budgets. Now what? All that’s left is trial and error testing of the tires that no one has much information on. Sure, I might be able to get some vertical spring rates, and maybe some cornering stiffness numbers, but longitudinal and lateral stiffness are critical to the way a tire responds, let alone absolute grip. And is it a Pacejka-based tire model, or a Magic Formula Tyre model, or one of the many other derivations out there? There are so many nuances that those models don’t effectively quantify, but they at least offer a starting point. Ultimately it comes down to getting as much feedback as possible from real-world racers, and applying what we know about tires to what knowledge they can share with us.
So how long does this process take? How much do I get to start with? The more data I get, the faster some stuff gets done, but that can also delay the process. If the wind tunnel data has one data point that’s not coincident with the equation, if the car has rubber bushings in the suspension, if the track performance isn’t in line with what the data is saying . . . Or say there’s NO DATA. Where do you start then? Contract to have CFD data done? Maybe you can find some dyno numbers and an established top speed, so you can get a drag number figured out.

Exhibit D: C6.R by Pratt & Miller or iRacing.com?
How long? For a car like the Solstice, the Spec Racer Ford or the Legends car — you know something with limited aero — it’s a fast three weeks or maybe a little more to establish performance limits before a public rollout. For a car with limited aero, likely five-six weeks, just to make sure the downforce numbers are reasonable outside the “normal” ranges. Aero dependent cars like the Dallara? Eight-twelve weeks might be necessary, just to verify that all the individual pieces are working as intended, and the handling is correct.
The big thing is, no matter how good the product is, it can always be made better. So keep your ears open, listen to what everyone says, and never settle for “good enough.”
* * *
A & C – Pratt & Miller (images by Wikipedia and Corvette Racing); B & D – iRacing.com (screenshots by Matt Orr and Bryan Heitkotter)